Advance customizes your structural pallet racking solutions to maximize available square footage and SKU slot facing to meet specific distribution needs. Flexibility and scalability are more important than ever to re-configure inventory diversification and meet current economic trends.

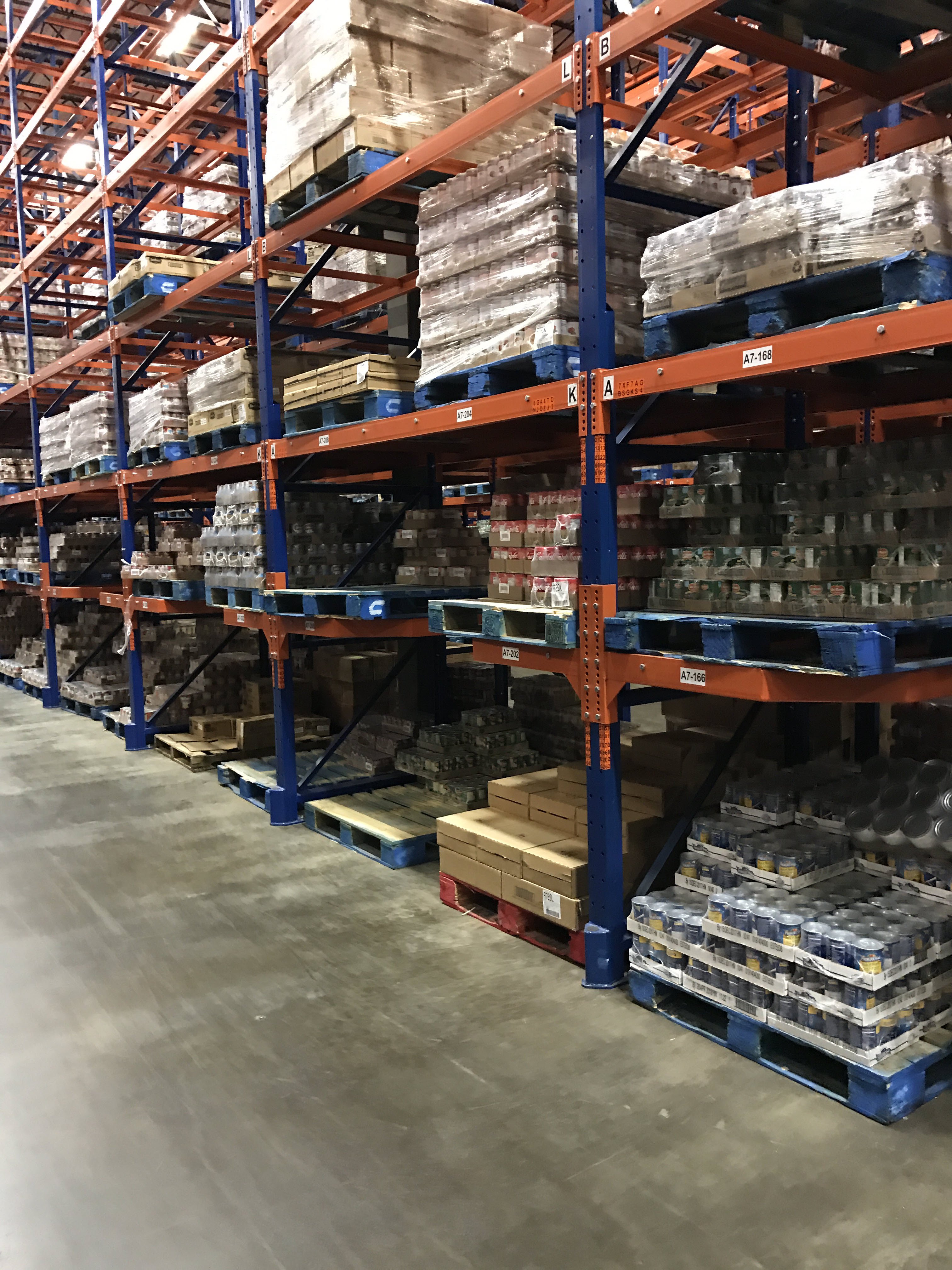


Food & Beverage Structural Pallet Rack Types
What is Pushback Pallet Racking?
Pushback racking is a type of pallet storage system that allows pallets to be stored on both sides of an aisle, providing higher density storage than other pallet rack systems. A pushback rack system is a LIFO system, normally composed of an inclined rail section that extends the full depth of the storage lane (typically from 2 – 6 pallets deep). There are a series of nested carts that the pallets rest on top of that roll on the rail system (either C channel or tube construction).
Selective Pallet Rack is a commonly used racking system, but not all racking systems are equal. ASP’s (Advance Storage Products) bolted structural pallet rack exceeds the RMI (Rack Manufactures Institute) racking standards of quality, long life and durability, as well as, the IBC (International Building Code) standards for structural design.
Selective Rack accommodates flexibility in slotting design, which is ideal for high turnover, high SKU stock count and quick product accessibility. Selective pallet rack is a cost-effective design allowing for the maximum number of SKU pick facings available in standard rack.
Store 2 pallet positions from a single aisle (4 pallets back to back) with the Double Deep Selective Pallet Rack. The rear pallet is accessed with a special fork truck with a pantograph extender. The Double Deep Reach warehouse racking system provides high-density storage at a lower initial capital cost when compared with other high-density storage systems.
Research the features of the Double Deep Reach pallet rack system to determine if it is the right industrial storage system for your application. Weigh the advantages and disadvantages of this racking system below.
Drive-In rack systems provide a low budget and high density storage solution for customers with lower SKU counts. Drive-In rack systems load from the back to the front (First-In Last-Out) as the forklift literally drives into the rack system, loads the pallet onto rails and backs out of the rack system. As the system is loaded rear to front, it must it be unloaded front to rear.
Drive-In systems reduce the number of aisles required in a warehouse. It is frequently used in cold storage applications, where the cost of (refrigerated) volume is at its highest and requires the most return on investment (more density).
Pallet Flow Racking:
Pallets are loaded into a storage lane from the loading aisle and flow downward on rollers towards the pickup aisle. When the pallet reaches the bottom, it is held by a pallet stop. As a pallet is unloaded from the bottom of the rack system, the next pallet flows down into place. Pallet speed is controlled by the rollers and brakes.