When distribution facility operators are looking to densify their storage layout (store up to twice as many pallets in the same facility when compared with selective rack), many times Pushback Rack systems can be an excellent alternative. A pushback rack system is a LIFO system, normally composed of an inclined rail section that extends the full depth of the storage lane (typically from 2-6 pallets deep). There are a series of nested carts that the pallets rest on top of that roll on the rail system (either C channel or tube construction). For a two deep system, there will be one cart storage position and the final pallet rests on the rail, for a three deep system there are 2 cart storage positions and one rail storage position, etc.
How does Pushback Work?
To operate a pushback system, the lift truck operator places the first pallet on the upper cart in the lane. With the second pallet the operator then “pushes back” the first pallet that is resting on the cart. The second pallet is then either placed on the rail in a two deep system, or placed on the next cart in a 3-6 deep system. This process is repeated until the lane is full. To unload the system, the operator removes the last pallet inserted (LIFO) and slowly backs out. The following pallets/carts roll forward on the inclined rail to the front of the system.
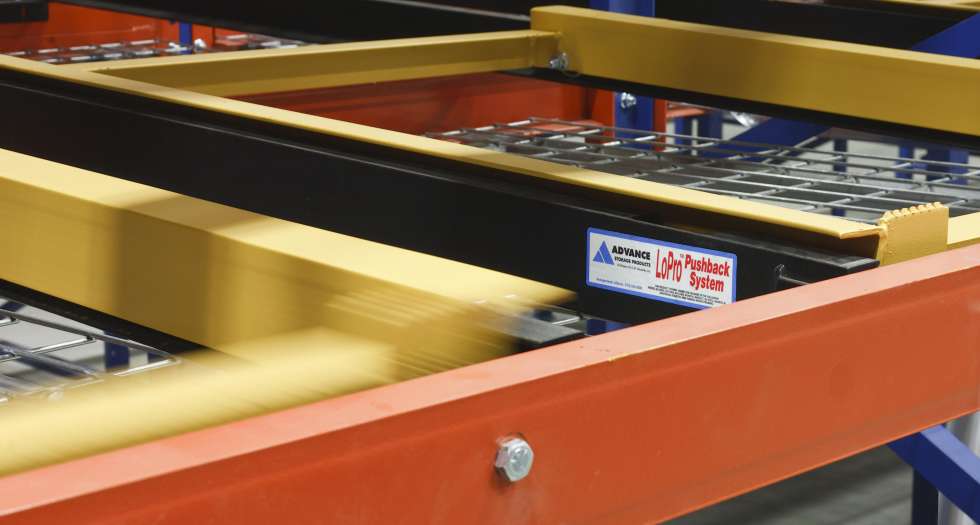
How to select the right depth of pushback?
One of the risks with any deep storage system is the risk of “checker boarding”. This happens when a deep lane storage system is selected, but there are too many individual SKU’s in the facility to efficiently fill the deep storage lane. For example, if you only have a single SKU of an item, and store it in a 6 deep lane, 5 positions of the lane are not filled resulting in 17% utilization of available storage capacity. Conversely if you have 50 pallets of the same item and store them in 9 lanes of 6 deep (54 available positions), the system will be 93% utilized. Most modern distribution facilities achieve better than 80% storage capacity utilization.
As a general rule of thumb, for pushback systems to be efficiently utilized, there must be roughly 4-5 times the number of SKU’s of an item in the facility than the depth of the storage lane. For example, if using 2 deep pushback, there should be at least 8-10 of the same SKU with in the facility, likewise for 6 deep to be well utilized, you would need 24-30 of the same SKU’s. Oftentimes facilities will be designed with a combination of different depths of storage (selective to 6 deep) to make best use of the floor space.
Pushback is used extensively in grocery, cold storage, consumer products, food & beverage and other industries where there are high pallet counts, mid-level SKU counts and a need to densify.