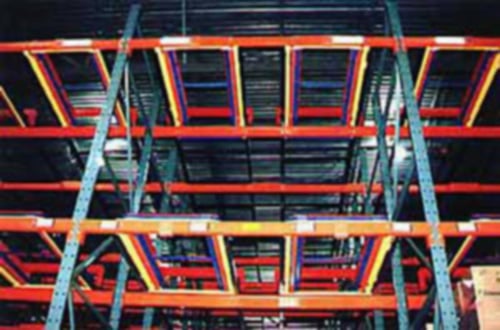
Quaker and Advance: The Right Mix!
Advance Storage Products was recently chosen to provide a storage solution for Quaker Oats’ largest single worldwide brand, its Gatorade thirst quencher. In total, Advance supplied more than 20,000 pallet positions of pushback rack to Quaker’s facilities in Indiana and Arizona.
Led by a number of strong brands including oatmeal, cereals, granola bars and pasta/rice mixes, the Quaker name has stood for quality products for more than a century. Acquired by the Quaker Oats Company in 1983, Gatorade has grown from sales of $100 million in fiscal 1984 to over $1.8 billion worldwide in 1999. Its Gatorade product line accounts for nearly 40 percent of the company’s sales and operating income, while commanding an 82 percent share of the sports beverage category in the United States.
As this division of the Quaker Oats Company continued its rapid growth, so did the company’s need for more efficient and dependable storage. Distribution centers continued to fill to capacity in an attempt to handle the company’s ever-growing product line. So, the team at Quaker put their heads together to find a solution to beat these skyrocketing storage and transportation costs. Quaker’s dilemma: How to improve the storage density of its facilities, while at the same time cutting back on product damage being caused by their current method of storage. There were multiple load presentation constraints due to new packaging. Over the years, Quaker’s floor stack environment had gone from storing four pallets high to only two. Another challenge was to provide greater SKU access (because of the stacking patterns, the customer was obligated to 27 units of one SKU).
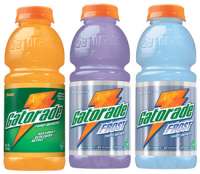
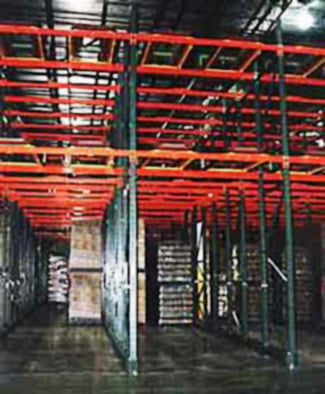
Advance’s solution: Advance 2, 4 and 5-deep Lo-Pro Pushback over floor stack. There were many factors to consider in order to justify the project and make it successful. Product mix was analyzed and a plan for slotting the system was developed prior to the completion of the installation. This was important so that systems could be set up prior to implementation, thereby not affecting order-picking productivity. A plan was implemented utilizing a combination of very dense Advance pushback racking for the large volume storage areas and more traditional selective styles for the case-picking areas. Result: Quaker’s productivity has improved, they are experiencing less product damage, they have increased the number of SKU’s being stored in the same area and they are enjoying dramatic savings to the facility previously incurred from outside storage and transportation costs. The project was completed without interruption of the company’s normal operations.